Creating a SDCI: Soft Digital Computer Interface
Spring 2022
This is a project that I performed with a group of undergraduate engineering students from various other departments. The project was sponsored by the Convergence Centre for Living Multifunctional Material Systems (LiMC2) and was assigned and delivered during the semester of Spring 2022.
We had the occasion to work side by side with Dr. Ryan Harne on his mission to create smart materials. Our goal was to realize a 3 bit mechanical interface to read force without the need of silicon that could be scaled using MEMS and replicated in soft materials.
Design
Our design simulates the bits of a modern computer using a system of complex gears where the speed of the gears determines the on and off of the single bit.
In this way we managed to convert the linear motion of a lever into fluid continuous binary code. To make the code discrete and remove the sinusoidal motion we added a spring based locking mechanism connected to the computing unit.
On top of the computing unit we placed a 3d printed circuit with copper tape that aligning for each bit, converts the binary mechanical value into a digital result that can be read by a computer.
Compared to piezoelectronics, this method of sensing mechanical forces consumes less power, is more sustainable and more economic. Further, this design can be realized with flexible materials, permitting more applications in multiple fields.
We had the occasion to work side by side with Dr. Ryan Harne on his mission to create smart materials. Our goal was to realize a 3 bit mechanical interface to read force without the need of silicon that could be scaled using MEMS and replicated in soft materials.
Design
Our design simulates the bits of a modern computer using a system of complex gears where the speed of the gears determines the on and off of the single bit.
In this way we managed to convert the linear motion of a lever into fluid continuous binary code. To make the code discrete and remove the sinusoidal motion we added a spring based locking mechanism connected to the computing unit.
On top of the computing unit we placed a 3d printed circuit with copper tape that aligning for each bit, converts the binary mechanical value into a digital result that can be read by a computer.

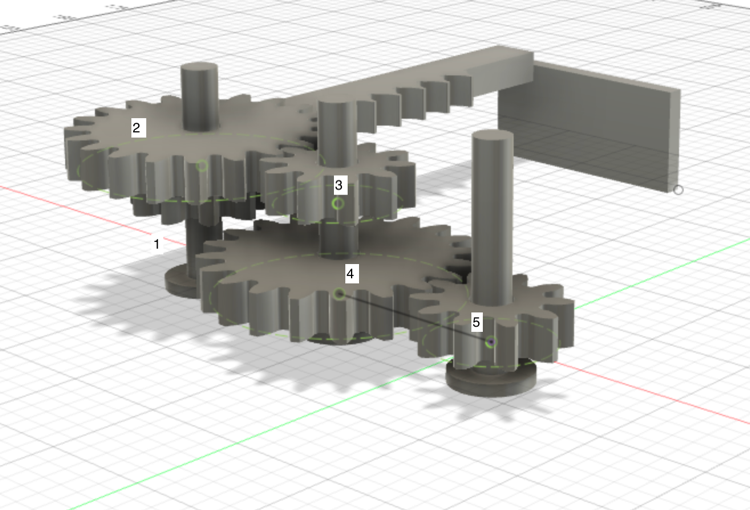
Advantages
Compared to piezoelectronics, this method of sensing mechanical forces consumes less power, is more sustainable and more economic. Further, this design can be realized with flexible materials, permitting more applications in multiple fields.